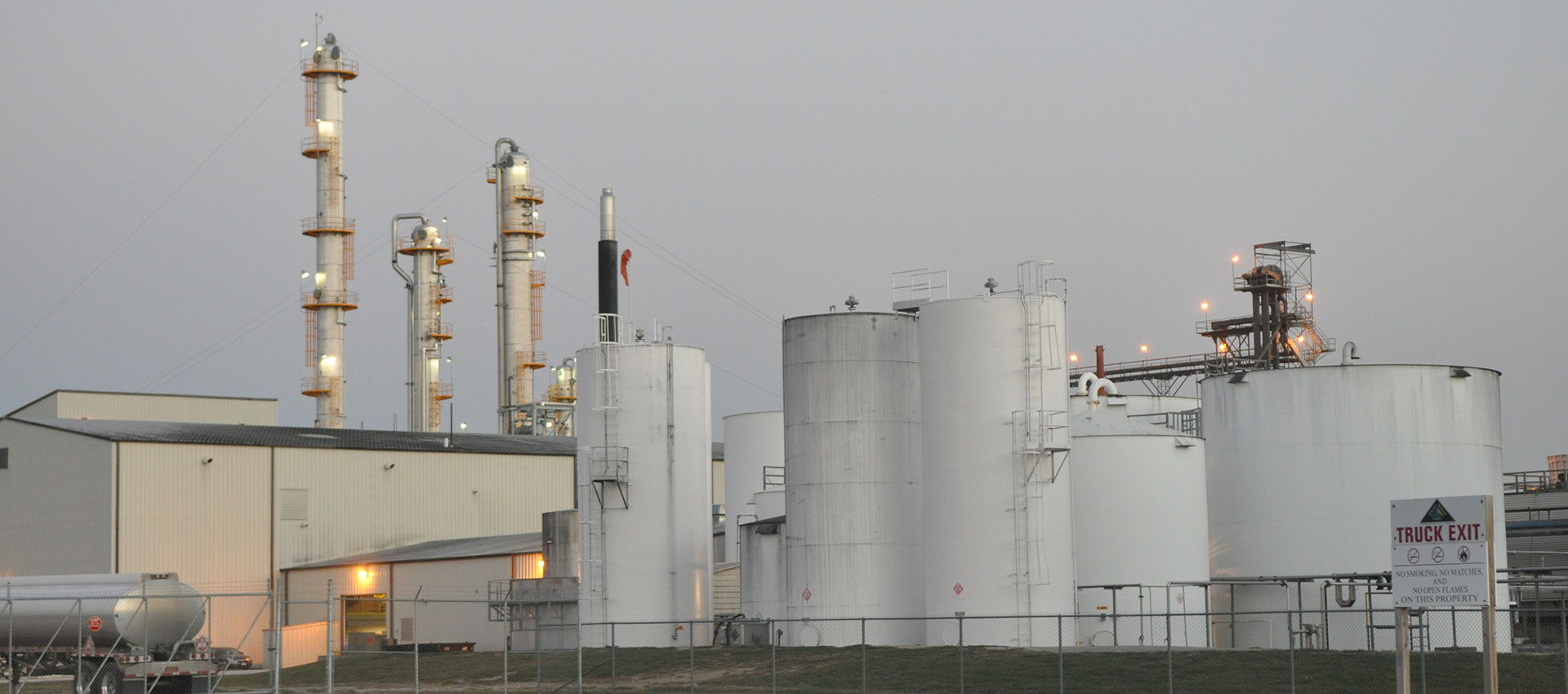
High Quality Alcohol
PROJECT SUMMARY
Opened in 2001, Golden Triangle Energy Cooperative (GTEC) produces ~20 million gallons of ethanol each year. In 2007, GTE contracted long-time partner Bachelor Controls (BCI) to retrofit its obsolete control system with a newer, more flexible system to meet future production and product expansion needs.
OBJECTIVES / REQUIREMENTS
GTEC charged BCI with retrofitting and replacing an obsolete control system with a newer, more flexible control system operating under the following parameters:
- retain all field wiring and field devices
- allow flexibility for day-to-day operational modifications and planned facility and product expansion needs
- ensure parts and technical support – including training – are readily available
- implement a system that has pool of skilled talent readily available to maintain/support the system
- maintain existing control functionality operating on newer, more current hardware
RESULTS / BENEFITS
BCI retrofitted the existing control system and replaced it in two phases – a pilot phase to test the implementation plan and device-control software modules under load, and a major implementation phase installed in only five days during a scheduled plant shut-down. The new system provided:
- current technology and hardware
- reduced installation costs by leveraging all existing field wiring and field devices
- maintained control functionality, plus built in flexibility for future facility / product expansions
- installed parts that are readily available from reliable distributors located near GTEC
- featured an open architecture with increased availability of training and maintenance support resources
- minimized down-time costs by containing major installation phase to only five days during scheduled shut-down
- improved efficiency of system control operations, so GTEC can focus on production and processing issues